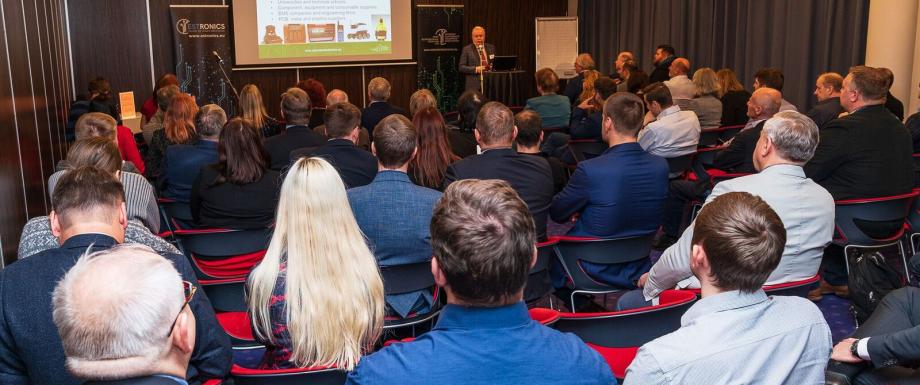
Electronics seminar 2018: Estonia has a world-class electronics industry
On November 29, the international electronics seminar in Tallinn brought together electronics industry representatives from all Europe to present the European electronics assembly industry and the possibilities of the Estonian electronics industry throughout the value chain. While experts analysed the development trends and future prospects of the electronics industry, Chairman of the Estonian Electronics Industries Association, Arno Kolk, shares his thoughts about the developments that have had the greatest impact on the industry in Estonia and internationally.
The international electronics industry has been using manufacturing services for decades. Typical examples are from the US electronics industry, in which many businesses, including space and defence industry companies, entrusted the assembly of electronic modules to specialised manufacturers in the 1970s. The production of computer modules was added in the 1980s.
What is less known is that the Estonian electronics manufacturing services (EMS) sector has a long history that dates back to the 1970s, when electronics units were set up at the Lääne Kalur, Harju KEK, Palivere EMT and other, mostly kolkhoz-related enterprises. These provided manufacturing services to many businesses, including Punane RET and the Institute of Cybernetics, but also for the Soviet space industry. Many of these enterprises are still operating in new forms today, and they continue to manufacture electronics.
Development of the electronics manufacturing services sector: step by step toward complete services
EMS is generally understood as a model where the assembly of electronic products and related functions are outsourced to specialised manufacturers. The area of responsibilities and scope of services offered by the EMS sector has continued to expand over time. Initially, it only performed simpler module assembly operations using components supplied by the customer (for example, surface-mount technology was once considered too complicated to be outsourced), then testing and the assembly of larger units up to the final product were added step by step, followed by component purchase, logistics services, etc.
Gradually, manufacturers acquired the competence to make complete products and their production processes were eventually often better than those of their customers, as the broad range of products and the constant pressure to improve efficiency had their effect. It was only a matter of time until assembly factories were involved in the development of production processes and trusted with designing production lines, fixtures and testing systems, and prototype manufacturing. They were also involved in product development, as the parallel development of products and production processes ensures quick market access and prevents unpleasant surprises during production.
The Estonian EMS sector also went through these stages – in 1997, Elcoteq Tallinn became the first factory in the world entrusted with the manufacture of mobile phones in consumer packaging. Indeed, Estonian EMS factories were involved in the development of production process and testing equipment 20 years ago.
Subcontracting has transformed into production partnership
While at the beginning, electronics were produced as “things in themselves,” i.e. end products (TVs, radios, telephones, etc.), an increasing share of electronic products are now integrated into other products, such as cars, planes, machinery, houses or even clothes. This means that while EMS customers were originally electronics companies, they now come from a wide variety of fields, from textiles and logistics to modern smart solutions.
Often, or even as a rule, these companies have no competence in the area of electronics manufacturing. Naturally, they could obtain such competences by acquiring an electronics business or building a new electronics factory. However, this is usually not economically justifiable, as the same resources can be used more efficiently to develop the core business while leaving electronics production to EMS experts.
This is why an increasing share of electronics manufacturing and development competences is becoming concentrated in EMS companies, and subcontracting is transforming into production partnerships where each business develops its key competencies. Many EMS facilities have developed product development capacities both internally and through a network of partners, so as to provide their customers with turnkey electronics solutions. Today, such solutions naturally involve various types of software. The electronics subcontracting industry has thus moved a long way from simple subcontracting and now covers a large part of the product lifespan from development to repairs.
Subcontracting or brand product?
It is often said that EMS factories should create their own brands and start developing, producing and marketing products under their own name. This is in fact a very common practice in China and other Asian countries, but not in the West. There is the exception of smaller firms, especially starter businesses that they are still looking for their niche and will accept any work in the beginning.
Larger businesses, especially those with many factories and large customers, have made informed strategic decisions in favour of the subcontracting model and have built their businesses accordingly. Making their own products would, as a rule, imply a quick loss of subcontracting customers and incomes, large investments in product development and marketing, and heated litigation over intellectual property. However, EMS companies can participate in product development in other industrial sectors and act as partners to firms in these areas.
It has also been argued that the Western industrial sector has no future and everything is made in China. The growth of the Chinese manufacturing sector has indeed been impressive and the electronics industry has its own role in it. However, European electronics manufacturing services have not disappeared at all ‒ quite the contrary. Customers value the quality, simpler communication and more flexible shipping that Europe offers. According to the leading EMS analysis firm in4ma, there are still over 1,300 EMS companies in Western Europe, which is four times more than in Eastern Europe. The West European EMS sector is also ahead in terms of turnover, even though growth is faster in Eastern Europe. There is therefore no reason to think that Estonia cannot or should not manufacture electronics now or in the future.
Estonian EMS companies and engineering firms form a strong industrial base that allows us, in cooperation with other sectors, to create and successfully export intelligent products of high added value.
The Estonian Electronics Industries Association is a modern, intelligent international network for experienced domestic electronics manufacturers, start-ups and international electronics businesses. More information: www.estonianelectronics.eu
Photo of Arno Kolk