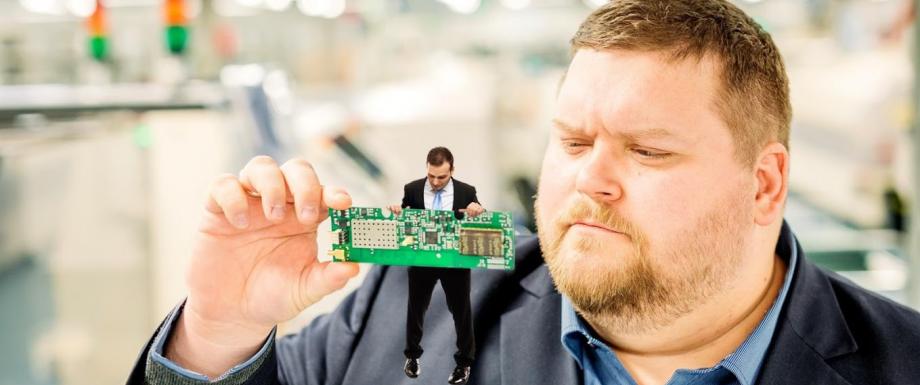
Incap is putting Saaremaa on the global map of high-tech production
Did you know that although the majority of our home electronics are manufactured in China, the electronics company Incap, based in Saaremaa, Estonia, produces electronics for the Chinese market? Only a few years ago, Incap was having to deal with large-scale redundancies, but now they have turned that around reaching doubled growth, and creating remarkably innovative solutions increasing the capacity of their factory robotics.
In Estonia, the Kuressaare-based electronics manufacturer Incap is primarily known for its many lay-offs making the news over the past few years. However, what many don’t know is that Incap, with its headquarters in Finland and factories in Saaremaa and India, was able to halt the decline of its Kuressaare factory, and is this year celebrating doubled growth achieved over the past year. The importance of Incap’s role among the producers and employers of Saaremaa is also indicated by the fact that the Kuressaare factory celebrated its 17th birthday this year.
Last year, Otto Richard Pukk took charge of Incap’s resilient international team and its 7,300 m2 factory. Pukk came to Estonia from Sweden, finally settling in Saaremaa, where his ancestors are from. “I’m glad to do my share and restore growth to the factory, so that we can put Estonia on the international map of the electronics industry again,” Pukk said explaining that while the general export trend in the Estonian electronics sector is going down, that does not apply to Incap. “We’re doing great!”
The 7,300 m2 electronics factory in Kuressaare is run by Otto Richard Pukk, who has returned to his roots after migrating from Sweden.
Innovation is compulsory
This spring, Incap opened a new SDM production line at the Kuressaare factory. At a cost of more than 1.3 million euros, the new line makes it possible to double the current production volume, and do the work of approximately 200 people, depending on what is being manufactured. According to Pukk, the new production line is another step towards industrial innovation, making it possible to adapt and supplement equipment as necessary.
“While we had been manufacturing PCBs on two lines, we now also have a third production line, which will double our current production capacity. One of the most significant aspects of the new line is that it is a rent-based finance investment. That means that our ability to provide clients with the most suitable products will become considerably more flexible: if necessary, we can replace or supplement different parts of the line after the completion of projects,” Pukk explains, confident that this production principle will soon be adopted in other factories as well.
Although Incap’s new production line can do the work of approximately 200 people, depending on what is being manufactured, doubling the previous production capacity, the company is looking for new employees because there are still jobs that robots cannot yet do without human intervention.
With its rent-based production line, Incap is currently a rather unique electronics manufacturer in Estonia. The Minister of Entrepreneurship and Information Technology, Urve Palo, who came to visit the brand-new line, also stated that the people of Saaremaa are helping to position Estonia more strongly on the global map of the high-tech industry.
Urve Palo, Minister of Entrepreneurship and Technology, visiting Incap’s new production line in Kuressaare. She was glad to see that Incap has kept pace with high-tech innovations for two decades, providing the world with the necessary technology under tough global competition.
Constant work to ensure competitiveness
With an area of 7,300 m2, Incap’s factory is currently the largest electronics factory in Saaremaa. The international team working on different projects for the Scandinavian region and other countries is 90 strong. At the Kuressaare factory, almost all of the information required for production and business operations is digitised, as is expected of a modern factory, making it easy to monitor and analyse.
Over the past year, the company has been able to grow thanks to mass production projects for established electronics manufacturers, as well as prototypes for start-ups. “We have acquired many new collaboration projects due to our small size: our clients have said that they consider the speed and flexibility of our small team to be a competitive advantage, and direct contact with us makes negotiations and decision-making simpler and faster,” Pukk explained.
The international team at Incap’s Estonian factory is 90 strong: working in three shifts, there are product assemblers, production line managers, business managers, as well as product testers, engineers and office workers.
To ensure production flexibility, the possibility of a flexible line set-up for different projects was the deciding factor. “The production line that was opened in spring is used to manufacture the most important segments of the electronic equipment we manufacture. For example, we can now attach up to 60,000 more components to PCBs every hour,” Pukk explains. “Purchasing a single-purpose line would be a rather risky investment in the current situation. At the same time, not updating our equipment could mean losing our market position. So, I’m happy to say that we have now found the way forward.”
Pukk considers the fact that the ISO 13485 certificate enables Incap’s factory to manufacture equipment for the medical industry as another competitive advantage: only a few Estonian electronics manufacturers have this certificate.
Made in China or Made in Estonia?
There are no limits to the products or product components currently manufactured at Incap’s Kuressaare factory: the unit manufactures the smart “brains” for the LED luminaries on Estonian streets as well as the contents of smart coffee cups for the Finnish coffee company Paulig. These cups accumulate energy from the warm drink, enabling them to communicate with each other. More than a million PCBs are delivered to customers annually from Incap’s Kuressaare factory alone.
Ismo Kyllönen, Production Manager at Incap’s Kuressaare factory, holding one of the solutions manufactured at this factory: the smart Bt.tn button, which can be programmed exactly according to your preferences. You can press this button to switch off the lights in a room, start a Skype call, or turn on the washing machine.
“Today, we are sending 90% of the output of the Kuressaare unit to Scandinavian companies. We also have clients from elsewhere in the world; for example, our furthest orders have travelled to North America and China,” Pukk explains. “It’s interesting that usually its Chinese electronics that are sold on our market, but we are manufacturing products for Chinese companies.”
Pukk explained that Incap’s Estonian factory is hoping to interest Estonian and North American start-ups who need to manufacture prototypes but are turning to Asia out of habit. “We can see that we are already competitive enough to sell electronics in China,” says Pukk, pleased with Incap’s collaboration with companies in China, encouraging Estonian start-ups to test local producers. “Our production chain does not include only manufacturing, but also everything else that is required: from engineering services to product testing and logistics solutions. For such a comprehensive service to be cheaper in Asia than in Estonia is just a myth now.”
Development depends on the team
According to Pukk, big things cannot be done without a team, which is why he makes sure his team members are happy and have development opportunities. In addition to their team of 90 people, Incap also offers seasonal work for students, collaborates with the students of Tallinn Polytechnic School and the local schools, trying to interest the next generation in engineering and electronics. “For example, we are looking for about a dozen product assemblers for the summer, if there are people without plans for July and August,” Pukk explains. “We like to see young people getting interested in engineering at an early age. For example, this year we became closely acquainted with KG Klemm, a robotics club at the Kuressaare Secondary School, which we also supported at the international student competition of LEGO robots in Denmark. We consider it to be of the utmost importance to help the development of this field,” Pukk states.
Incap’s attempts to develop and create an environment suitable for innovation was recently also recognised by the Ministry of Social Affairs, who included Incap in a group of 40 companies applying for the label of family-friendly entrepreneur. Pukk admitted that although the training for many positions at the Incap factory takes place on site and does not require previous specific know-how, it is nevertheless somewhat complicated to find employees in Saaremaa. “While we did lure one local employee, it is significantly more difficult to get employees with families to come over from the mainland,” he explained.
Every year, a million green PCBs leave Incap’s Kuressaare factory – but the new production line will double its production capacity. During an hour, it is now possible to add up to 60,000 more components to the PCBs.
And although Incap’s current production lines mainly consist of robots – including the recently opened SMD production line – Pukk thinks that there are many areas where it is not possible to replace humans, and where new team members are welcome. “I hope we can find new talent from Saaremaa and the mainland: we are constantly sharing information and job notices in the press and social media,” Pukk explains. In order to be closer to part-time employees, clients and start-ups, Incap has joined the Spring Hub in Tallinn, with a little office on the premises.
“Having doubled our growth according to the economic indicators as well as the number of team members, gives us a clear vision of future projects and allows us to share the following message – the difficult times are behind us, and the only way is forward,” said Pukk summarising Incap’s future plans, after having been selected to the board of the Estonian Electronics Industries Association last spring to promote the entire Estonian electronics sector.
Read more about Incap here. Follow Incap in Facebook and LinkedIn.