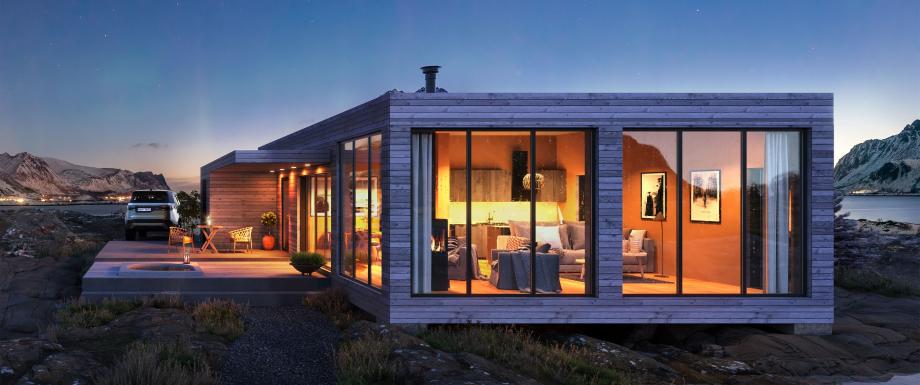
Standardized modular construction solutions and carbon footprint: How are they related?
The construction of new buildings is moving more and more from construction sites to factories, and the main advantages of this are quality and a predictable final price. Modular buildings are particularly well suited to those areas of the country with a smaller number of companies offering construction services, a desire to erect buildings at a faster pace than usual, or greater labor mobility associated with the opening of a new factory.
Ready-made modular building construction projects for real estate developers
In cooperation with Scandinavian partners, we have developed standard solutions to produce various types of modular buildings. Now, our selection includes holiday home-type private houses and apartment buildings of various sizes. Semi-detached houses and terraced houses produced from standard modules will be added to the selection soon.
Timbeco standard modular buildings are suitable for larger residential real estate development projects, where there is a desire to erect similar or even different types of buildings at a rapid pace. The erection of a modular building is increasingly turning construction sites into assembly sites, and this is significantly less disruptive to the surrounding environment than traditional construction methods.
Speed is important
In the case of building projects from standard modules, there is a very short time from an idea to a turnkey solution. This is an excellent solution in case of a rapidly growing need for housing or in the event of a revival in the real estate market, when many projects are still pending, but the market demands new housing immediately.
Building from modules is many times faster compared to traditional site construction. It is possible to simultaneously carry out work both on the construction site and during the construction of modules in the factory. While the construction of the foundation and the installation of communication systems are carried out on the plot, the interior finishing works of the modules and the installation of furniture are underway at the factory.
Thanks to the finishing materials offered as a pre-selection, which have proven themselves in the target markets, it is possible to save valuable time and money. It is possible to install kitchen and bathroom furniture, wardrobe systems and sanitary equipment in the factory to minimize work on site as much as possible.
We provide developers with project-based marketing materials to simplify the sales process and make purchasing a new home as smooth and pleasant as possible for end customers. Our marketing package includes 3D images of each building that correspond to the location of the building, a catalog of interior finishing materials intended for the end customer, LCA (life cycle assessment) calculation of the building, video and image material from the production and installation of buildings, etc.
Life cycle assessment of a building
At a very early stage of the project, we conduct LCA analysis of the modular building to identify the carbon footprint of the building. For the Norwegian market, we make calculations according to the NS 3720 standard and the TEK17 environmental declaration, and in Sweden BREEAM SE NC 2017. As a result of the analyses, it is possible to apply the principles of low-carbon construction from a very early stage of the project.
Most of the buildings manufactured and erected by Timbeco are at least class B according to the LCA calculation. Thanks to the detailed LCA analysis and the selection of building materials with a smaller carbon footprint, we are also able to offer class A modular buildings. To achieve this, a balance must be found in terms of environmental footprint and reasonable construction cost. For example, buildings made of lighter construction materials have a smaller carbon footprint than heavier buildings. The number of recycled materials in building constructions also reduces the size of the environmental footprint. For example, the environmental footprint of glass wool is 50% lower than that of rock wool. If possible, in the project, we use finger-jointed wood material in the frame and in the joists, we install interior finishing materials produced from renewable resources or based on the circular economy principle, etc.
We are also seriously thinking about the end of the life cycle of the building and creating opportunities for the buildings we produce to be in use for as long as possible. Timbeco's wooden buildings are designed in such a way that the materials/parts of the building can be easily dismantled, easily repaired, and reused. Modular buildings are designed in such a way that their purpose of use and technical systems can be changed in the future, if necessary.
Long-term benefits
During the last few years, I have implemented several standard module projects both in Norway and Iceland. Soon, we will be ready to offer similar solutions in other European markets as well.
With our services and products, we want to offer sustainable solutions that benefit both customers, home buyers and the surrounding environment. We believe that successful and long-term cooperation is the goal for all parties.
As a result of the cooperation, we want to create well-planned, visually beautiful, and interesting buildings that are part of a modern, happy, and diverse urban space where people want to live.